Diacore case studies
Gravetye Manor -
East Grinstead
We were required to track saw new door openings through some 400-750mm deep brick and stone walls and demolition lines through a concrete slab to enable subsequent vibration free breaking out by the groundwork sub contractor.
These works, together with the diamond drilling of various service holes, ensured the integrity of the surrounding structure was maintained.
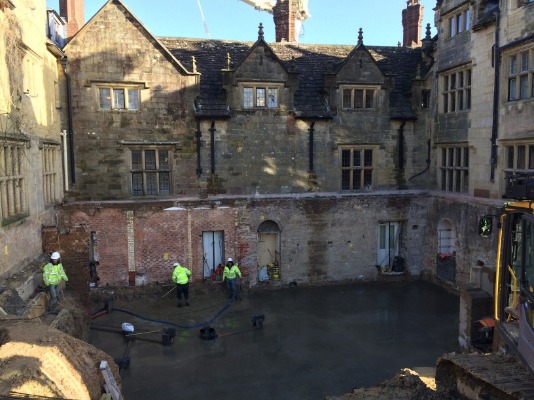
Chalvey Road Bridge – Slough Road
After the top section of the bridge had been hydro blasted, we were requested by our clients, Balfour Beatty, to add 6no. drainage weep-holes which were 1m deep drilled from below with hydraulic drill motors.
We then carried out concrete repairs to the bridge itself using Weber Repair Mortar.
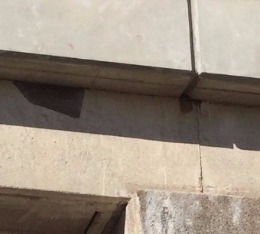
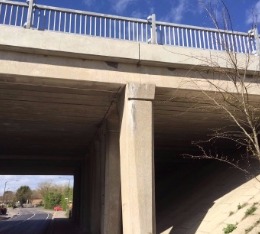
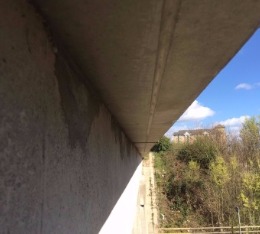
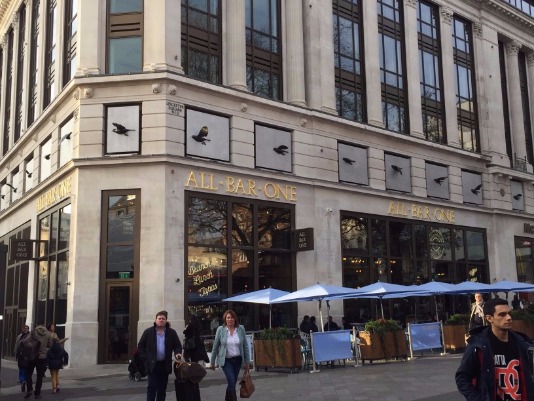
All Bar One – Leicester Square
Drilling small diameter holes for the power supply for each letter of the signage. Consisting of 18mm diameter cores through stone, 2 no. RSJs 20mm thick and 800mm deep brickwork.
Abingdon School
Demolition of a World War II Air Raid Shelter.
The shelter was located next to the Head Master’s house, so we needed to complete the work quietly.
Drainage holes were drilled into basement slab.
The concrete was crunched into small pieces using a Husqvarna demolition robot and Dada crunching jaws. The spoil was used as the base of the new entrance road in the same location.
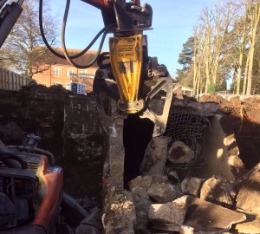
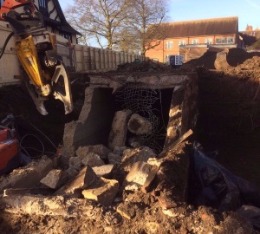
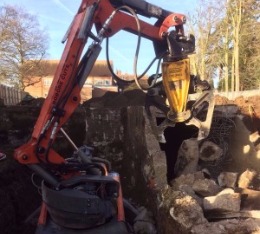
Barking Riverside
BRIEF
We were asked by our client to stitch drill 350mm diameter openings in a suspended jetty slab, ensuring that the cores were not dropped into the river below. We achieved this by drilling a daisy wheel stopping each core 10mm short and supporting the centre on a fixed bar, then we removed the central core out through the top of the opening.
The openings were then handed over to the client to carry out investigation works below the wharf.
Once the client had finished with the openings we were asked to infill them again, we needed to secure H16 Rebar to strengthen the repair before infilling with Fosroc Patchroc 250. Again, all without dropping anything into the river and without access from the underside of the jetty.
METHOD
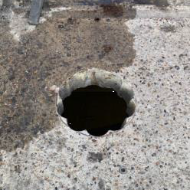
1. Stitch drill 350mm diameter openings, whilst retaining the cores.
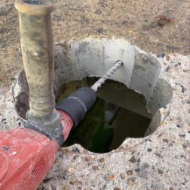
2. Percussion drill into the side of cored concrete.
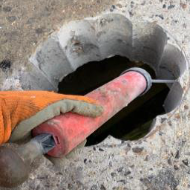
3. Clean out the drilled holes.
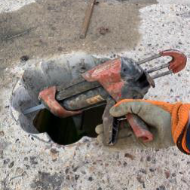
4. Insert Hilti RH500 injectable resin.
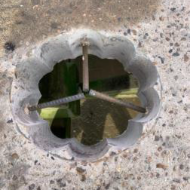
5. Embed H16 bars into the resin.

6. Prepare the formwork.
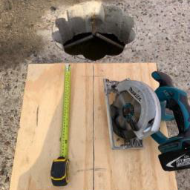
7. Cut into 2no. sections.
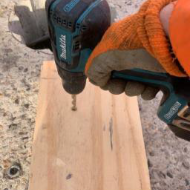
8. Drill the securing holes.
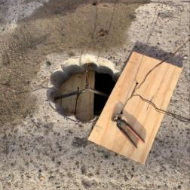
9. Wire tie 1no. section of formwork.
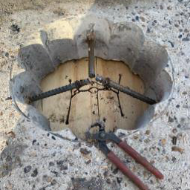
10. Wire tie second section of formwork.
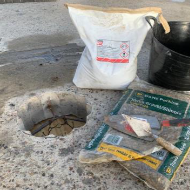
11. Mix Fosroc Patchroc 250 2/3 with 1/3 pea shingle.
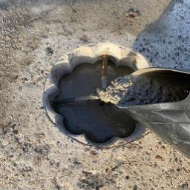
12. Pour onto formwork.
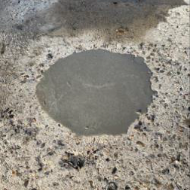
13. Trowel off top surface.
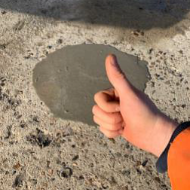
14. Job done, onto the next hole.